Fiberglass "A Gateway to Green Building Innovation"
Fiberglass Rebuilding Cleveland's Historic Landmarks
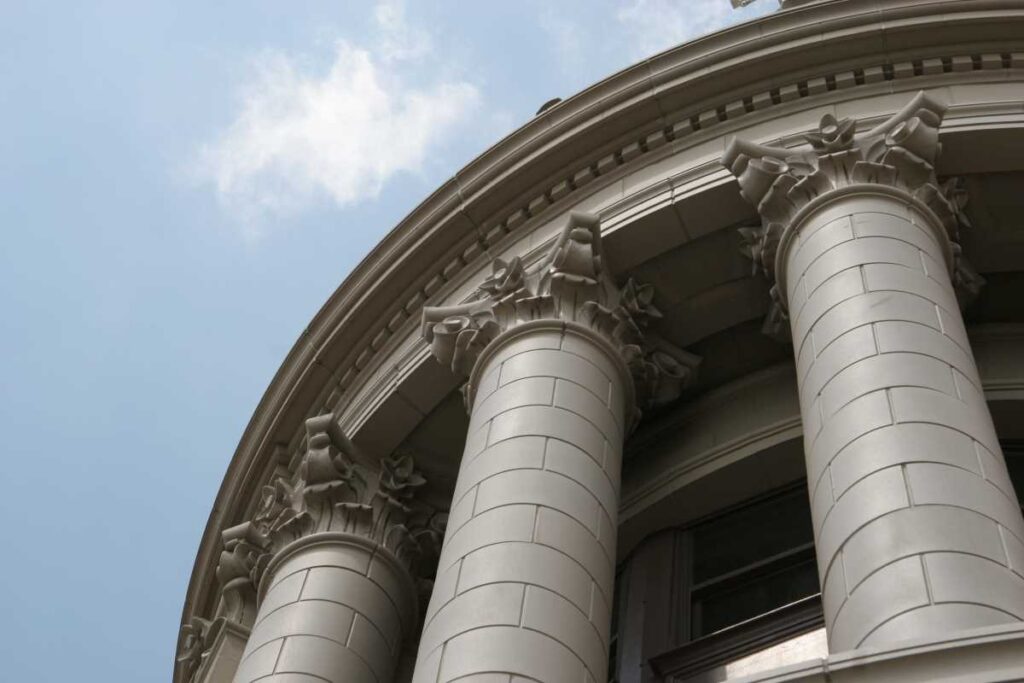
Terminal Tower, 49th floor fiberglass dentil cornice and corinthian columns replacing terra cotta.
Restoration and new construction projects using Fiberglass Reinforced Polymer (FRP) composites is fast becoming a viable alternative to traditional building materials. The ability of fiberglass to reproduce shapes and sizes of complex configurations allows designers the freedom to recreate historic shapes and finishes without sacrificing the authentic look.
Restoration projects using fiberglass products are gaining further popularity and opening the eyes of owners, builders, architects, engineers, and developers. The restoration market for FRP has not yet blossomed anywhere near its potential. This is due to the unawareness of the benefits of FRP and the lack of specialized fiberglass manufacturing companies. Cleveland’s own Architectural Fiberglass, Inc. (AFI) has been providing architectural elements throughout the country for over 20 years. “Our education efforts to the construction industries have been convincing architects and contractors the long-term benefits of FRP” says General Manager Mike Dobronos.
And AFI’s efforts are becoming visible, because as one looks around Cleveland, there is a lot of fiberglass being installed all over the city. Chances are you have seen AFI’s fiberglass in action masquerading other materials on restoration projects downtown such as the W.T. Grant Building, The Huntington Bank Building, and the Keith Building. Mike says “Sometimes we send architects out to look at projects and they come back asking where the fiberglass is because it impossible to differentiate from the material it is mimicking”. AFI produced hundreds of square feet of decorative terra cotta on the West Technical High School restoration. Individual damaged terra cotta units were replaced with fiberglass replicas. It was less expensive and faster to replace the terra cotta with FRP, rather than repair and re-glaze the damaged terra cotta units. FRP elements are scattered throughout the building façade. Except for the installing contractor, no one else really knows were the 250+ fiberglass units are installed.
When St. Peter’s Church on 17th and Superior was restored, engineers realized that the 155-year-old structure would never be able to support a new belfry tower that was removed in the 1920’s after a fire damaged the church. AFI reproduced the original 65′ tall by 28′ wide fiberglass tower that housed three of the churches original massive bronze bells. An architect later asked how such large stones were erected at such a height. Easy, when using fiberglass panels that are about 200 times less weight than real stone.
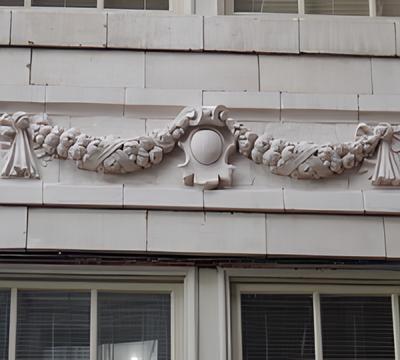
West Technical High School Restoration, Decorative fiberglass scroll elements.
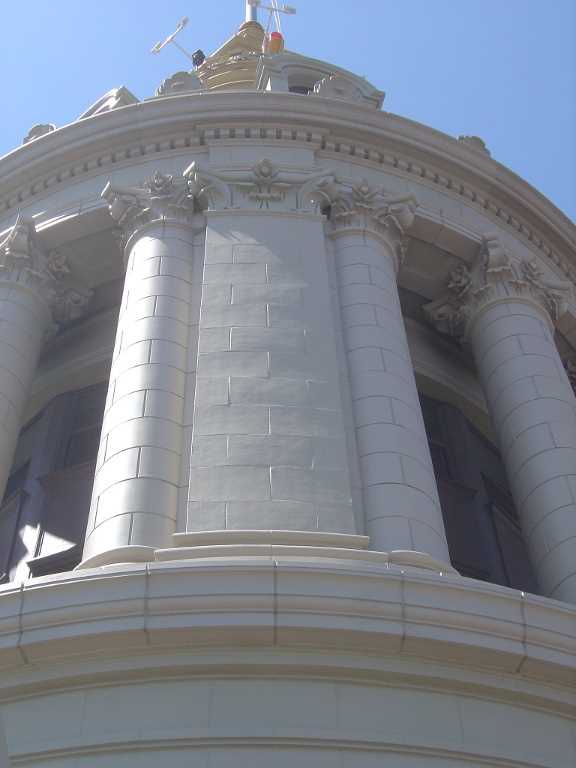
Terminal Tower, 48th and 49th floor fiberglass dentil cornice and Corinthian columns replacing terra cotta.
AFI replicated the textured stone/brick patterns with false mortar joints consolidating multiple individual stone elements into larger fiberglass panels. The fiberglass units were pieced together like a puzzle and mapped out on detailed shop drawings provided by AFI. The fiberglass joints were filled with a sealant that contained aggregate to simulate mortar. The FRP panels matched the decorative brick pattern design of the existing church structure below.
More recently, AFI has been contracted for the ongoing makeover of Cleveland’s 80+-year-old Terminal Tower. Authentic looking fiberglass has already replaced thousands of square feet of terra cotta including 32 columns that are 40″ dia by 30′ tall that surround the tower at heights over 600 feet. Hundreds of lineal feet of specialized cornice for several floors have been replaced with fiberglass including a cornice at the 15th floor that spans over 10 feet in height. In as little as 12 weeks, AFI can make custom molds from the existing terra cotta and deliver pieces to the site that cannot be distinguished from terra cotta originals. The lightweight fiberglass replicas are brought into the building up freight elevators to the appropriate floor for installation. Fiberglass eliminates the need for cranes or other massive structures that would be required for terra cotta replacements. The 32 columns that AFI produced for the project cost about the same as 4 new terra cotta columns with lead-times that would have exceeded over one year.
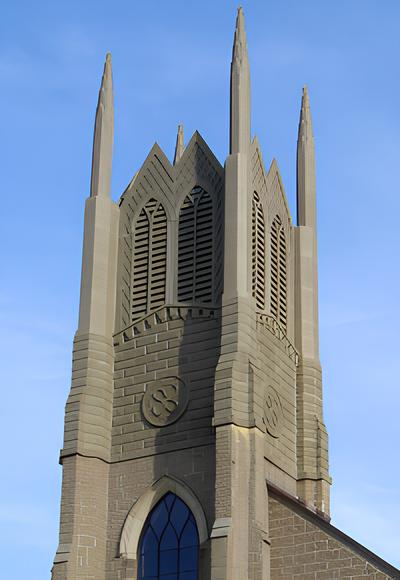
St. Peters, 65′ tall by 28′ wide fiberglass belfry replicating stone on existing building below.
Fiberglass on New Construction
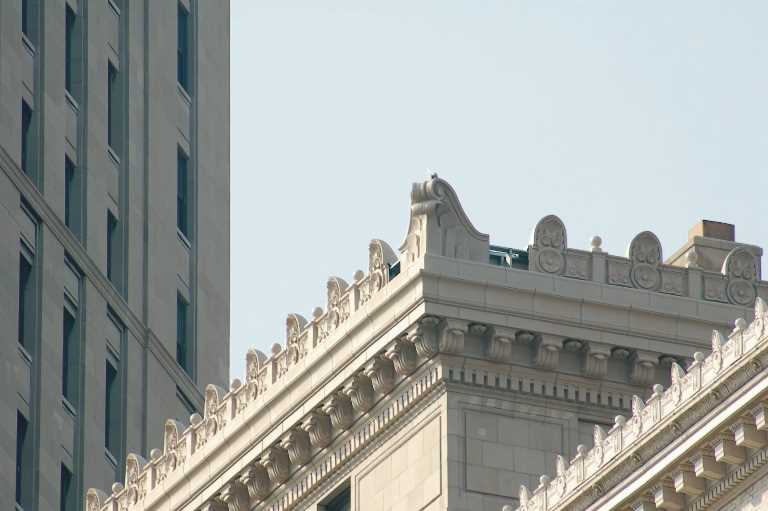
Terminal Tower 15th floor, 10′ tall fiberglass cornice replacing terra cotta cornice.
Though frequently associated with old buildings, many of these distinctive fiberglass elements are also incorporated into new structures, especially bank, university, library and government buildings. Local new construction projects outfitting AFI’s fiberglass materials include massive 48″ diameter columns at Western Reserve Academy in Hudson; Fiberglass cornice and columns used to mimic stone to eliminate the need for heavy support framing at the Elyria Municipal Courthouse; And new fiberglass dentil cornice replicating limestone at Kent State University Franklin Hall was manufactured at a fraction of the weight, replacing hazardous limestone cornice that was falling off the building.
AFI replaced The Akron Beacon Journal 25′ tower which was designed, fabricated, and erected in less than a few months to replace the old rotating sign that was near collapse. AFI manufactured the architectural art deco design matching the original Indiana limestone building.
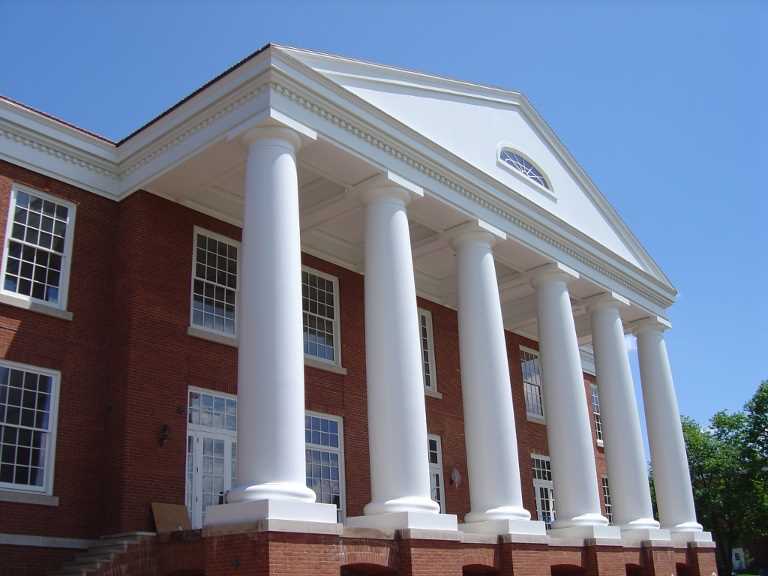
Western Reserve Academy, Hudson OH, 48″ dia by 28′ fiberglass
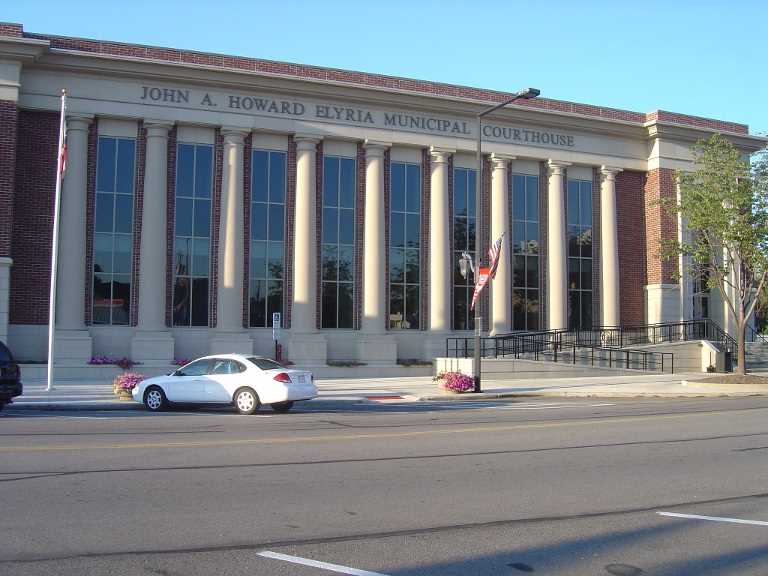
Elyria Municipal Courthouse, 40″ dia columns and cornice replicating stone.
The tower now includes the latest high tech electronics and is a new focal point for downtown Akron. Individual fiberglass panels clad a new steel frame that supports the structure. Fiberglass was chosen because of its light weight and ability to reproduce the complex shapes in an efficient and economical manner. Decorative stone elements were cost prohibitive and the existing frail structure could not support the weight. The fiberglass elements enabled the project to be completed in less than 7 months from concept to completion. Reworking the tower with stone would have cost $700,000 to $800,000, rather than the $75,000 in fiberglass.
Recent new construction projects touting AFI’s fiberglass include Garfield Middle School, Cleveland State University Law Building, John Carroll University Dolan Center, and the Fireman’s Memorial between Cleveland Browns Stadium and the Great Lakes Science Center.
Since AFI’s birth, they have assembled thousands of stock molds that can be reused to build a massive variety of columns, cornice, balusters, cupolas, domes, fascia panels, finials, moldings, sculptures and other decorative elements. Some of AFI’s well-known customer base includes a variety of hotel chains, Disney, and Major League Baseball.
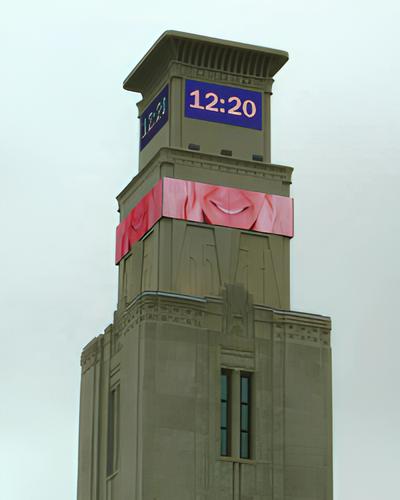
Akron Beacon Journal, 25′ tall by 13′ wide Fiberglass Tower replicating Indiana Limestone.
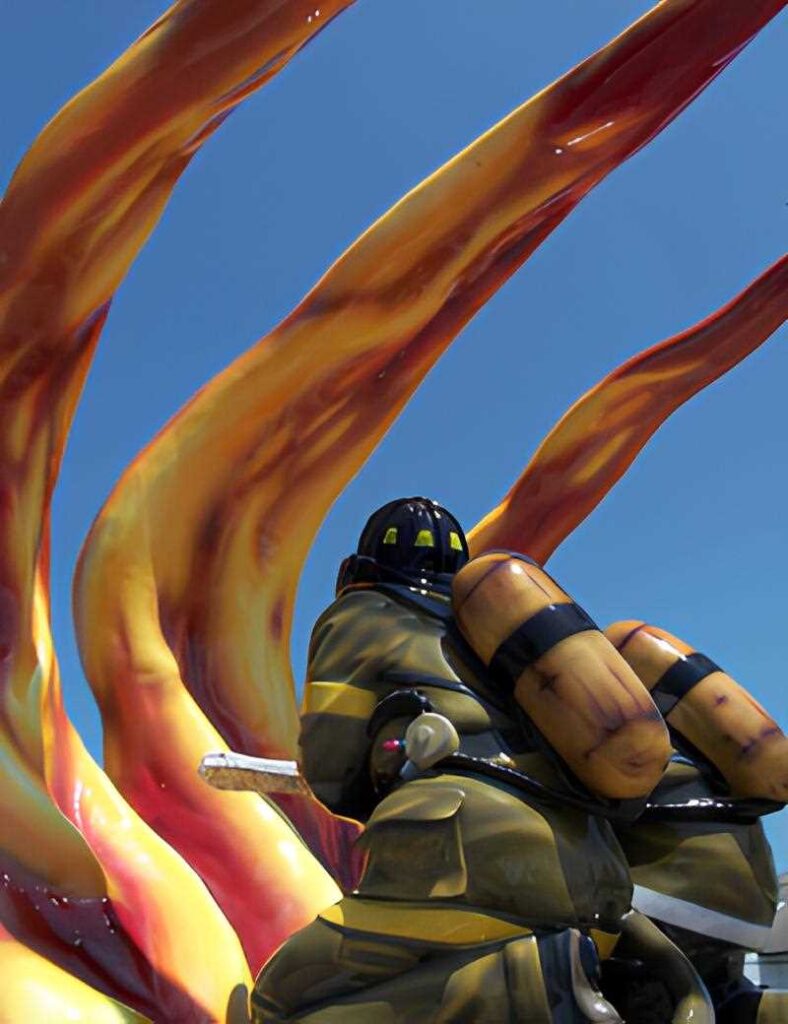
Building Green With Fiberglass Composites
Green building has become an increasingly important focus for new construction. When fiberglass is compared to other traditional products such as concrete or terra cotta, the total life cycle assessment of fiberglass material contributes to Green Building contributions such as the LEEDS Program (Leadership in Energy and Environmental Design). When the impact of the energy consumed to produce a given product, the installation of a product, and the environmental sustainability is taken into consideration, fiberglass products use far less energy than other traditional materials. Fiberglass can be used in ways that are less energy and carbon intensive than other building materials.
Processing cement for example, requires mining, extraction, and burning of raw materials that emit ample amounts of carbon dioxide. Once the cement is processed, It can require up to 90% more cementitious material to produce the same product from fiberglass. Not only does the cementitious product require more material, but it also wieghs far more than its fiberglass counterpart. The light weight fiberglass contributes to overall savings due to lower transportation costs, faster construction thereby causing less distress and disruption to the community, less dead weight requiring smaller and lighter building structural requirements, and less heavy lifting equipment. The overall carbon footprint for fiberglass throughout its life cycle is far less.
FRP is often chosen over other construction materials as environmentally sustainable and having a life cycle that exceeds other products. Fiberglass is not only a low maintenance, long lasting durable product, but also is resistant to rust, rot, and corrosion. By doubling the useful lifespan compared to other products, fiberglass’s durability reduces the need for replacement, repair, or repainting which makes it more earth friendly. The durable nature for FRP products reduces the overall negative environmental impact. Fiberglass is unaffected by termites and its use as a replacement to wood virtually eliminates toxins from exterior painting and pesticides.
Other Fiberglass Advantages
The new innovative technologies and molding techniques make fiberglass indistinguishable from authentic materials. “Fiberglass is not just a shiny white plastic looking material similar to a boat hull or fiberglass shower surround” says Mike Dobronos. Fiberglass can be molded into a number of different finishes to mimic wood, stone, terra cotta, concrete, steel, granite, copper, and other popular building materials. Finishes can range from a smooth dull matte to a high gloss polished look, or a slight texture to rough stone texture. FRP parts are chosen over other material because it is lightweight, cost effective, corrosion resistant, and is virtually maintenance free. Fiberglass products are manufactured with fire-retardant resins and the color and finish is molded in the surface. Because FRP begins with liquid polymer resins and formable glass fibers, the finished shape can be curved, corrugated, ribbed, or contoured in a variety of ways, with varying thickness. Per unit of weight, FRP is among the strongest commercial material available. Pound for pound, FRP is stronger than concrete, steel or aluminum.
Though fiberglass is very practical when compared with the material, maintenance and installation cost of other traditional materials. One should not assume that the material cost of fiberglass is low, but the installation methods and procedures boast lower installed cost and lower life cycle cost. Stone or terra cotta decorative ornaments can become dangerous when a building’s supporting structure deteriorates to carry the load of a solid, heavy material. Usually stone or terra cotta features require additional robust framing and attachment areas. Fiberglass elements typically weigh 1.5 to 2.5 lb. per square foot; and can be attached to a building without heavy steel supports or structural rehabilitation of the attachment areas on a building. Intricate details that are molded into fiberglass such as brackets, medallions, steps, drip edges, and curves add rigidity and strength to fiberglass elements. In most cases minimal pressure treated wood blocking or galvanized steel studs is sufficient for attachment.
Contractors love the fact that fiberglass is so lightweight, it in turn lowers their all around installation cost and it is easier to install than traditional materials. Fiberglass ornaments can be easliy screw-fastened, bolted, or hung onto a concealed clip system. Usually at 3/16-inch typical thickness general-purpose scaffolding and manual placement of fiberglass materials is sufficient. General contract workers and carpenters are frequently capable of installing fiberglass without heavy lifting equipment and cranes.
Fiberglass on Historical Landmarks
Fiberglass is gaining substantial recognition with preservation and landmark agencies as they are realizing the advantages and are accepting FRP as a viable alternative to traditional materials. Preservation agencies are skeptical at first but after seeing examples and samples of fiberglass, it is a convincing and faithful alternative to more costly and less durable materials. In most cases using traditional materials is cost prohibitive, and it is difficult to find companies qualified and able to produce such decorative materials. Historic landmarks have been repaired or replaced with fiberglass elements including the rear façade of The White House, home to U.S. Presidents and countless other Colonial and Victorian restoration projects.
The Future of Fiberglass
AFI and the American Composites Manufacturers Association (ACMA) have made great strides with the introduction of FRP to the International Code Council (ICC). ACMA is the largest trade association serving the composites industry and ICC is the organization that publishes the International Building Code (IBC) that is the primary model building code used throughout the United States. Before 2009 FRP products were not recognized in the IBC and fell into the category of plastics limiting its uses on building facades. ACMA’s Architectural Division developed, and submitted a code change proposal to the ICC. The proposed code change added a specific section for FRP Composites into the IBC which addressed several end-use applications, and provides test requirements and regulations for the FRP industry. Through the exhaustive ICC public hearing process, the ICC approved and adopted ACMA’s proposed code changes that will be published and will be effective in the 2009 IBC. This code change is a significant step towards recognition of FRP Composites by the prescriptive building codes of the USA.
AFI has recognized the use of FRP in all phases of construction and has undertaken the task of informing and educating contractors, architects, and developers the benefits of fiberglass. At this time there are no clear, long-term life expectations of fiberglass. This is because fiberglass products have been installed on buildings for more than 60 years, with no significant sign of deterioration. For more information about fiberglass products please contact Architectural Fiberglass, Inc.