Fiberglass Reinforced Plastic (FRP)
What is fiberglass?
In its simplest form, Fiberglass Reinforced Plastic (FRP) is a material system consisting of a plastic resin matrix, glass fiber reinforcement and suitable additives. Mud and straw is an example of a form of composite; the mud acts as a resin matrix while the straw is the reinforcing fiber. These composite materials are combined and processed by one of a number of methods to meet certain performance and appearance requirements as a finished component or composite. Fiberglass allows for greater design flexibility previously prohibited by the limitations of traditional building materials. Fiberglass is non-corrosive, strong, lightweight, maintenance-free and can be erected efficiently and economically. Per unit weight, fiberglass is among the strongest commercial materials available. Pound for pound, fiberglass is stronger than concrete, steel or aluminium.
Fiberglass (FRP) Properties
Typical Fiberglass
Properties-
Flexural strength: 16,000 to 32,000 psi
-
Flexural modulus: 0.8 to 1.4 x106 psi
-
Tensile strength: 9,000 to 18,000 psi
-
Tensile modulus: 0.8 to 1.4 x106 psi
-
Elongation: 1.0% to 2.5%
-
Compressive strength: 15,000 to 25,000psi
-
Impact strength izod: 4 to 12 lb./in. of notch
-
Specific gravity: 1.0 to 1.8
-
Density: 80 to 110 lbs./ft.3
-
Continuous heat resistance: 150 to 350
-
Thermal Coefficient of Expansion: 12 to 20 in/in/Fx 10-
-
Barcol hardness: 40 to 60
A typical 1/8" glass mat laminate
using specific fire retardant resin properties-
Flexural strength: 28,000 psi @ 77 degrees F
-
Flexural modulus: 1.07 x 106 psi @ 77 degrees F
-
Tensile strength: 16,800 psi @ 77 degrees F
-
Elongation: 2.2%
-
Elongation: 1.0% to 2.5%
-
Barcol hardness: 45 to 50
-
Glass content: 31%
-
Specific gravity: 1.62
-
ASTM E-84 (tunnel test): <25
-
UL Subject 94: V-O
Our Fiberglass
Our typical fiberglass parts are a nominally 3/16″ thick laminate in a fire-retardant Class 1 resin with exterior gel coat finish. Because our fiberglass begins with liquid polymer resins and formable glass fibers, the finished shape can be curved, corrugated, ribbed, or contoured in a variety of ways with varying thickness. Per unit of weight, our fiberglass is among the strongest commercial materials available. Pound for pound, fiberglass is stronger than concrete, steel or aluminium. Fiberglass parts can be delivered to the site ready to be installed. At times, our fiberglass product may be assembled in our shop and transported via truck, ready for installation.
Our price may include: custom tooling, parts, shop drawings, packaging, freight, lightning protection and connectors, support structures and attachment hardware. Installations may also be included as part of our total package.
Our Optimum Design
Our typical laminate is composed of the following:
Gelcoat
The molded-in surface coat that contains the color and is resistant to ultraviolet attack and airborne contamination.
Resin
Various resins that can be formulated to meet specific physical requirements: weatherability, heat resistance, chemical resistance, fire retardancy and electrical properties.
Integral Reinforcements
In the form of cores, stiffeners and attachments can be molded into the laminate to produce any performance requirements.
Fiberglass
Fibers of glass that reinforce the plastic (polyester resin). By varying the glass content, we can affect the strength and mechanical properties of the laminate.
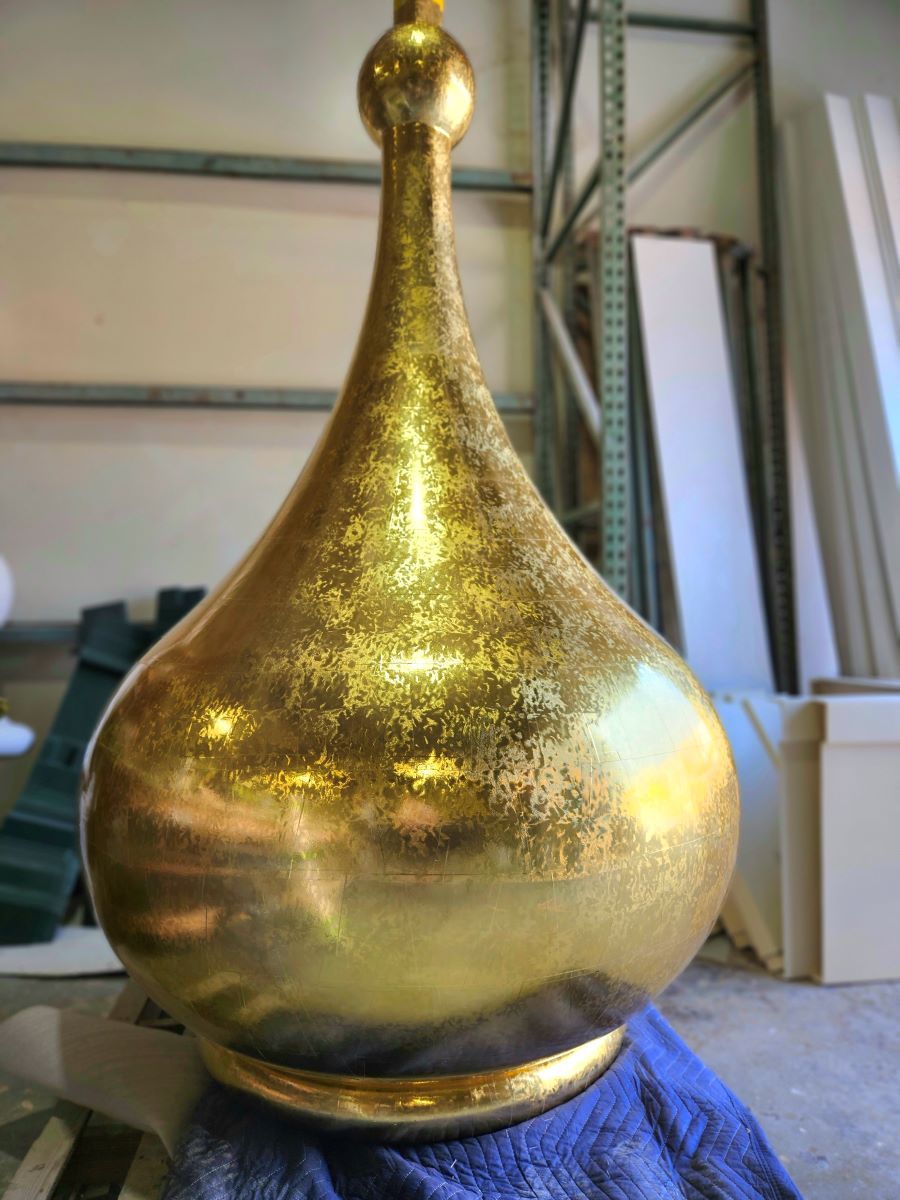
Gold Leaf Process
In addition to fabricating simulated fiberglass gold finishes, Architectural Fiberglass, Inc. also manufactures products with actual gold leaf. Our gold leaf process is a significant technological break-through when compared to cheap imitation golds that fade to silver and/or delaminate within a few years. Our proprietary gold leaf process has been used on decorative fiberglass products for over 20 years with no sign of deterioration or discoloration.
The process involves genuine 22 karat gold that is permanently bonded at extremely high heat onto the underside of a clear film called Tedlar (a DuPont product made of polyvinyl fluoride). The Tedlar film is resistant to chemical corrosion, ultraviolet light, saltwater, solvents, cleaning agents, and physically protects the gold to prevent top surface abrasion. Tedlar carries a 10 to 14 year life warranty against fading or delamination on glass, metal, painted wood, plastic and other common substrates. Regarded by architects as one of the most durable surface protectors, Tedlar has long been used as a standard outdoor protective laminate for 25 years. The gold is under-sealed with a premium grade pressure sensative acrylic adhesive.
In a nutshell, you have the ultimate gold leaf process. The manufacturer of the gold guarantees the 22 Karat gold process against wear and fading for 10 years.