Fiberglass Cornice (FRP)
Fiberglass Cornice (FRP)
For fiberglass cornice drawings, visit our download page.
Cornice is the molded or decorated projection that forms the crowning feature at the top of a building wall and/or other architectural element. Specifically, it is the uppermost of the three principal members of the classic Entablature, which includes the Cornice, Architrave, and Frieze.
The term is also employed for any projection on a wall that is provided to throw rainwater off the face of the building.
In modern architecture, cornice is usually used for decorative reasons rather than functional. It does at times drain water towards the building roof, away from the building into gutters mounted on the outer edge of the cornice, or there can be cornice and gutter combinations draining water into gutters that are concealed by the cornice.
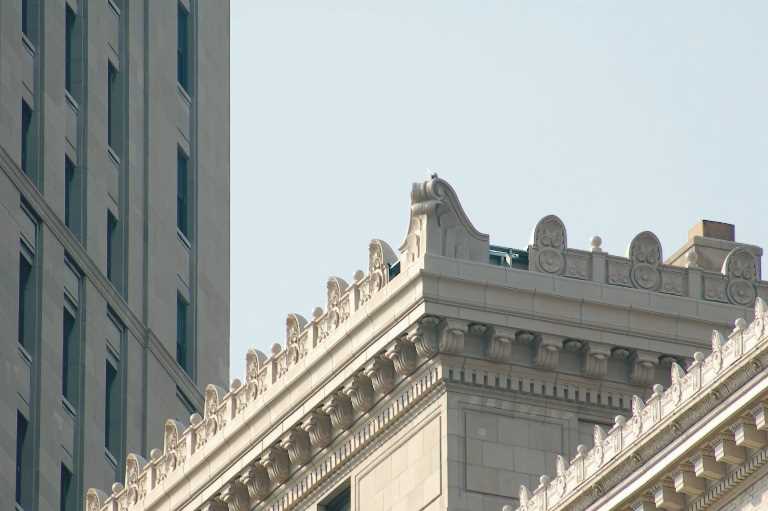
Fiberglass Cornice and Finish Appearance
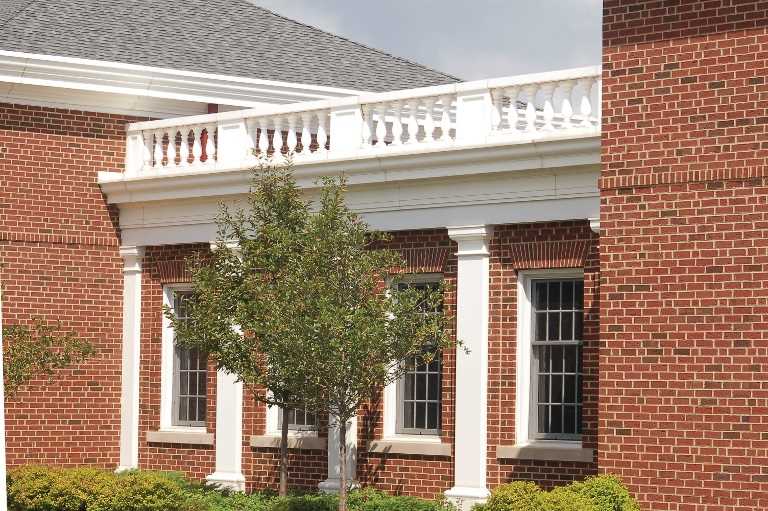
The most commonly used gel coat for exterior architectural applications is UV-inhibited NPG (neopentaglycol) isophthalic gel coat, which gives the best resistance to weather and UV light.
Gel coat can be customized to match any color, or other decorative elements on the building, or the caulk that will be used to seal joints between sections. Many times other additives are introduced to our fiberglass cornice manufacturing process to replicate these other materials.
Metallic flakes, granite, glass, and natural stone aggregates are commonly incorporated into the finish of cornice for the desired results. Cornice sections can be sandblasted or manufactured with slight differences in colors to mimic the weathered and random colors of stone. Weathered metals such as copper with green/blue patinas are common also common fiberglass finishes.
When fabricated properly, custom finishes will be indistinguishable from the authentic material.
Architectural Fiberglass, Inc., has no standard color or finish chart to choose finishes. Every project is a custom match and seldom are two projects the same. We usually request a sample of the authentic material from the designer and match the fiberglass to the original material.
Finishes are not limited to molding techniques but to the scope of the designers imagination. Fiberglass cornice moldings have become one of the most popular uses of architectural fiberglass. Not only for its ease of use, but fiberglass cornice can be manufactured to replicate most finishes including cast iron, terra cotta, limestone, sandstone, marble, granite, copper, steel, wood, sheet metal and other popular building materials. Finishes can range from a smooth dull matte to a high gloss polished look, or a slight texture to a rough stone texture.
Fiberglass Cornice Installation and Cost Considerations
Fiberglass cornice is very practical when compared with the material, maintenance, and installation cost of other traditional materials. One should not assume that the material cost of fiberglass is low, but the installation methods and procedures allow for lower installed costs and lower life cycle costs. In addition to new construction, fiberglass cornice is widely used for restoration of old cornices made from terra cotta and cast stone. Stone cornices and other decorative features can become dangerous when a building’s supporting structure deteriorates to carry the load of a solid, heavy material. In new construction Glass Fiber Reinforced Concrete (GFRC) or stone features require additional robust framing and attachment areas.
Fiberglass cornice typically weighs 1.5 to 2.5 lb. per square foot and can be attached to a building without heavy steel supports or structural rehabilitation of the attachment areas on a building. Intricate details that are molded into fiberglass such as brackets, medallions, steps, drip edges, and curves add rigidity and strength to the cornice system. In most cases minimal pressure treated wood blocking or galvanized steel studs are sufficient for attachment. The fiberglass cornice can be screw-fastened, bolted, or hung onto a concealed clip system. Fasteners should be galvanized, stainless steel or non-corrosive. Usually at 3/16- to 3/8-inch typical thickness, installation with general-purpose scaffolding and manual placement of cornice is sufficient.
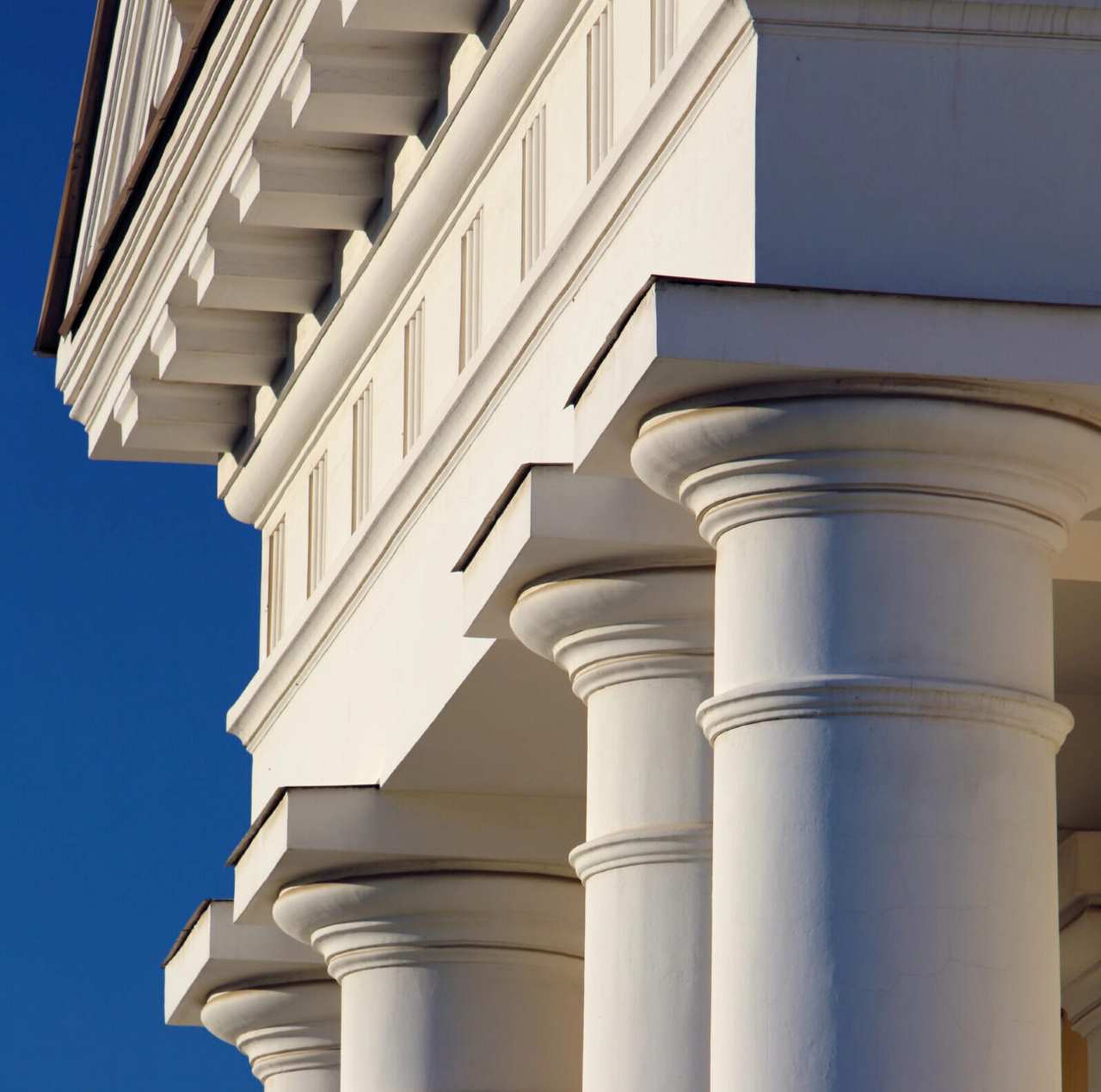
Easy Installation for General Contractors and Carpenters
General contract workers and carpenters can frequently install fiberglass cornice without heavy lifting equipment and cranes. FRP cornice offers a wide range of design options.
Versatile Design Options
Connection details, support structure, panel size, and panel shape vary substantially. Our preferred mounting method involves placing the cornice on the face of a building with an integral cornice “roof” pitched downward to shed water. This integral “roof” increases the surface area and material cost of the fiberglass but eliminates the need for any internal framing system. By eliminating a framing structure, we save on labor and material costs associated with building custom framing for the fiberglass cornice.
Structural Integrity and Framing Options
The structural integrity of fiberglass cornice itself can usually maintain the profile, eliminating the need for an internal framing structure. Other methods involve connecting to a framing system or attaching just under the eave of the building roof. If the eave supports the cornice, no framing system is needed. When framing is required, less expensive materials can create the cornice roof. Plywood with roofing material and/or flashing suffices. During the design phases, we should consider labor and material costs for the most ideal situation.
Ideal Cornice Section Sizes
The ideal cornice sections range between 4- to 10-feet long and 12- to 70-inches tall. When fabricating cornice to simulate stone or GFRC, a 4-foot section resembles a stone cornice with a joint every 4-feet. To facilitate installation, we can manufacture the same fiberglass cornice in an 8-foot section with a false joint in the middle, giving the same overall appearance. Although additional mold costs accompany a longer 8-foot section, lower installation costs should outweigh the mold cost.
Joint Configurations
In the design phase, we should also consider the joint configuration. “Lap” joints and “butt” joints or a combination of the two generally adjoin sections together. With a “lap” joint, one edge of a section overlaps the edge of an adjoining section. One edge steps down while the adjoining cornice section edge remains flat, overlapping the stepped edge. This joint treatment allows the cornice to be cut in the field to exact lengths. Sometimes a “lap” joint does not include a “roof,” reducing the overall cost of the fiberglass. However, the lack of a cornice “roof” and the need for internal bracing may increase overall installation cost.
With a “butt” joint, the sections have returns that meet but do not overlap.
Usually our “butt” joint returns the full profile of the cornice including the “roof” adding considerable strength to the fiberglass cornice and eliminates the need for internal bracing. There is an increase in fiberglass material cost but usually an overall lower installation cost.
Joints between fiberglass cornice sections should be between 1/4- to 3/8-inch to allow for thermal expansion. Fiberglass expands and contracts similar to metal, and approximately twice as much as stone or steel. Joints should be filled with a good quality polyurethane or silicone flexible sealant to allow for movement but create a watertight joint.
Corners, rake pediments, and other irregular details on buildings should also be considered when installing fiberglass cornice. Miter cutting cornice in the field is ill-advised and not recommended. We prefer to factory manufacture inside, outside, and irregular corners for the installer. If only a few corners are needed, factory mitered corners can be made in our facility. The corner seam is finished and reinforced with fiberglass. When quantities dictate, factory molded corners can be manufactured for the project. To facilitate the installation, corners and adjoining sections are numbered, diagramed on drawings and pre-fit at our facility before shipping to the site.
Origins of Cornice
The Cornice
The Cornice undoubtedly had its origin in the primitive eave projection: the Greek Doric and Ionic cornices recall early wooden roof forms, and the Egyptian cavetto-and-fillet cornice is a derivation of the overhanging papyrus stalks that formed the eaves of primitive shelters. The cornice lost its structural significance early on and became a stylized decorative element. In the Greek and Roman eras, it assumed firmly standardized forms in the classical orders that were retained, with variations, through the Renaissance and later periods. As an element in the classical entablature, the cornice is composed of the cymatium, or crown molding, above the corona, the projecting flat member, which casts the principal shadow. In this shadow, and supporting the corona, are a group of moldings called the bed molds, which may be elaborated with dentils. The Corinthian and Composite cornices are further embellished with modillions, or brackets, under the corona. The soffit of the Doric corona is decorated with square, flat projections called mutules, having guttae, or small knobs, hanging from their lower surfaces.
The Entablature
The Entablature is the entire unit of horizontal members above the columns or pilasters in classical architecture – Greek, Roman or Renaissance. The height of the entablature in relation to the column supporting it varies with the three orders, Doric, Ionic, and Corinthian; but in Roman and Renaissance interpretations it is generally about one fourth the column height. The entablature’s component members are the architrave which rests directly upon the abacus, or top member of the column cap; the frieze; and the cornice, or topmost member. Essentially, the entablature is a development from the primitive lintel, which spans two posts and supports the ends of the roof rafters. In Renaissance and modern designs, the entablature is also used upon a wall as the crowning member or as a horizontal band, irrespective of columns.
The Architrave
The Architrave, in architecture, is the principal beam and lowest member of the classical entablature, the other main members of which are the frieze and the cornice. Its position is directly above the columns, and it extends between them, thus carrying the upper members of the orders. The term also applies to molding around the sides and top of a door or window frame.
The Frieze
The Frieze, in architecture, is the member of an entablature between the architrave and the cornice or any horizontal band used for decorative purposes. In the first type, the Doric frieze alternates the metope and the triglyph; that of the other orders is plain or sculptured. The 5th-century BC treasury of the Cnidians at Delphi shows figures in the frieze. Roman and Renaissance examples, a notable one being on the 1st-century BC temple of Vesta at Tivoli, display acanthus leaves and other ornamentation.
Fiberglass Cornice Pricing
Fiberglass cornice pricing is based upon all aspects of the project and is not as simple as providing a per linear foot price on a profile. Cornice pricing requires measurements of the overall length, height, and depth of the profile including dimensions of brackets, dentils, or other decorative features that may be part of the profile. Ideally, a full set of detailed architectural drawings would be required. At a minimum, drawings that indicate dimensions or that are scalable and show a section view, elevations, and overall roof plan are required.
All aspects of a project need to be considered such as all inside and outside corners, or other irregular conditions associated with the cornice. It is also important to determine if the top of the cornice is to be fiberglass or if it will be fabricated with traditional materials such as plywood and metal flashing. Without knowing all aspects of the project, it will likely be substantially underpriced, requiring a change order later. All the mold/tooling conditions need to be considered to price and fabricate the cornice system accordingly.
Our cornice gallery

































Download Drawings and Specifications
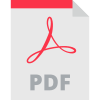
Cornice
(2.12 MB)
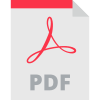
Cornice Details
(384 KB)
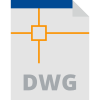
Cornice
(2.98 MB)
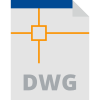
Cornice Details
(455 KB)
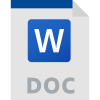
Fiberglass Cornice Specifications
(2.98 MB)
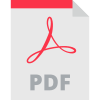
Cornice
(2.12 MB)
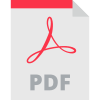
Cornice Details
(384 KB)
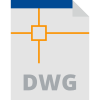
Cornice
(2.98 MB)
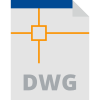
Cornice Details
(455 KB)
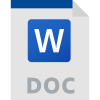
Fiberglass Cornice Specifications
(2.98 MB)