Builders Exchange Profile
A Builders Exchange Member Company Profile, Builders Exchange Magazine
Fabricating building parts lets workers understand
The joy of creating
Architectural Fiberglass, a national player in its specialized niche, is making inroads into the regional market by touting FRP’s advantages
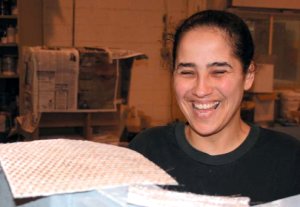
Workers at Architectural Fiberglass enjoy the fabrication of pieces to go on some of the nation’s most unusual structures.
Architectural Fiberglass Inc., a designer and fabricator of decorative fiberglass-reinforced plastic (FRP) ornamentation for both restoration and new construction, is one of only a few such companies in the area. “What we do, there are only few companies that can do it,” says Mike Dobronos, president of the firm. “We work in 40 states. But the market here in Cleveland is just beginning to blossom for the product.”
The firm began 15 years ago with the manufacture of domes and cupolas for religious, civic and commercial institutions. It, like so many other good ideas, was born as the solution to a problem, when the founder, Mike Dobronos, was faced with a deteriorating aluminum dome on his own house of worship. After thorough research, he decided that fiberglass would be the best material to use to rebuild the dome — and that his own firm would be the best one to do it.
In 1999, the company opened its own manufactory on the East Side of Cleveland to create the building parts. Since its birth, it eventually was able to assemble thousands of stock molds that can be reused to build a massive variety of columns, cornices, balusters, cupolas, domes, fascias, finials, moldings, louvers, pilasters, sculptures and other parts. The large assemblage attests to the growing popularity of the material, and to its versatility.
A tour shows not only the collection of past work, but workers busily involved in creating a host of new pieces. It’s worth a trip. Suited to decorative applications where it would be prohibitive to hire an artisan to work in more traditional materials, FRP has been used to create everything from the onion domes of Orthodox churches to the Middle Eastern architecture of mosques and other religious buildings, as well as the Art Deco ornamentation of 1930’s buildings. Visitors to AFI can see everything from giant baseball gloves to gilt angels.
Special effects
The many attractions in the World of Disney show how imaginatively FRP can used to create theme decorative elements, as can the Taj Mahal Casino in Atlantic City, an AFI project. Indeed, Las Vegas has been called the architectural fiberglass capital of the world, due to the great variety of architectural effects that FRP has been called on to reproduce there. FRP offers exact specifications with unlimited possibilities, without repetition. “The Disney quality control specs are very, very strict,” says Steve Dobronos, the founder’s son. “But that is one of the clients that helped us get started. Now, people put us into their specs.”
Architectural Fiberglass provides customers with designs, drawings, patterns, molds and parts. The work is specific enough to take a special skill. “We train our own people, so they come with no preconceived habits,” says Steve Dobronos. However, they do only fabrication, not installation work, due to a lack of time. “We used to be installers, and we can recommend them,” adds Mike.
“Cornices and columns become easy to install,” he goes on. The FRP elements are prefitted by AFI and numbered for ease of installation. Noncorrosive fasteners such as masonry screw bolts and clips can attach the pieces directly to the building. Gaps between the piece and building itself are sealed with silicone caulk or elastomeric polyurethane.
FRP is versatile enough to match existing structures in both color and texture. “Architects send us stuff and we match it,” says the senior Dobronos. “We don’t have a color chart. We build what people want us to mimic. You can see it, and you don’t know that it is fiberglass.”
Fiberglass can be any shape, size or appearance,” he goes on. “It’s not just white plastic.” It can be curved or contoured and then finished to mimic wood, stone, terra cotta, concrete, steel, marble, granite, or copper. Columns and balustrades can be made as load-bearing parts to hold weight, or as covers to wrap around structural supports.
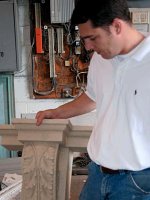
Steve Dobronos shows off some of AFI’s work.
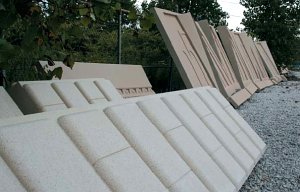
In the yard at AFI can be seen pieces to go on many buildings, including the new Akron Beacon Journal clock tower.
FRP pieces are less expensive to use not so much because they are in themselves more economical, says Mike, but because they are so much lighter and thus easier to place and fasten, without the need for heavy scaffolding, cranes or specialty workers — general workers can do the work. the lighter weights also do not need heavy structural supports or structural rehab.
Thus, their light weight makes them easier to install, cost-effective, corrosion resistant and almost maintenance free. Fiberglass weighs less than two pounds per sf of surface area, and can be produced to be watertight. Pound for pound, it is stronger than concrete, steel or aluminum. Domes can be up to 40 ft in diameter, up to 60 ft high. FRP also does not rust or rot, and it’s heat- and chemical resistant and fire retardant.
Coatings also vary. Many area churches have domes and other ornamentation that shine with 22-karat gold safeguarded by Tedlar, an Architectural Fiberglass Specialty. Gold flake gel coat is another ecclesiastical option. While UV-gel coats do not need paint, and molded in surface gel coats are resistant to airborne contamination, it can suffer some aesthetic UV degradation, uniformly, if coated in a dark color. And its light weight means that pieces must be fastened securely, and if used in areas accessible to the public, they will find it hard to the touch but acoustically hollow sounding when struck. FRP has been used for 50 years with no significant sign of deterioration.
The creative process
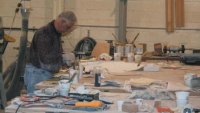
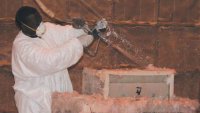
At AFI, the fabrication of a structural element takes many steps. It all begins in the pattern shop, where the company makes a mold to create the product. The gel-coat is introduced into the mold to provide color, and then resins are used as a matrix strengthened with fiberglass reinforcements. Cores, stiffeners and attachments can be molded in to produce special performance needs.
FRP in action
Let’s take a look at some of AFI’s work on local projects. FRP has been used in new construction, such as Crocker Park and John Carroll University’s Dolan Hall, as a cost-effective alternative to create almost any look.
It can also be seen in rehabs such as the W. T Grant Building in downtown Cleveland, on the Keith Building’s 19th and 20th floors, or on the West Technical High School rehab into apartments. And when the 65-ft by 28-ft St. Peters Church at 17th and Superior was rehabbed recently, it was found that the building was too frail to hold the weight of stone replacement pieces. AFI was called in by the structural engineers to create the right components. Later on an architect had to ask how the crews got the stone up that high. Easy, when it’s not stone. In Hudson, the columns at Western Reserve Academy were so wide, the school turned to FRP as an affordable, beautiful substitute.
Another project where FRP came through was the new Akron Beacon Journal Tower, 12 ft square by 28 ft tall, in which the eight original, but too often revamped, light beacons had to be recreated as something more authentically Deco. “We like to do things that take more doing, like this,” says Mike, about the replacement of the stone and steel with the visual artistry of FRP. It is the challenge that thrills him, the versatility of his chosen medium, and the pure joy of creation.