Towering Achievement
This article appeared in Properties Magazine, August 2009 issue.
Extensive renovation program revives Downtown Cleveland landmark
By Lou Kren | Photos by Ken Krych
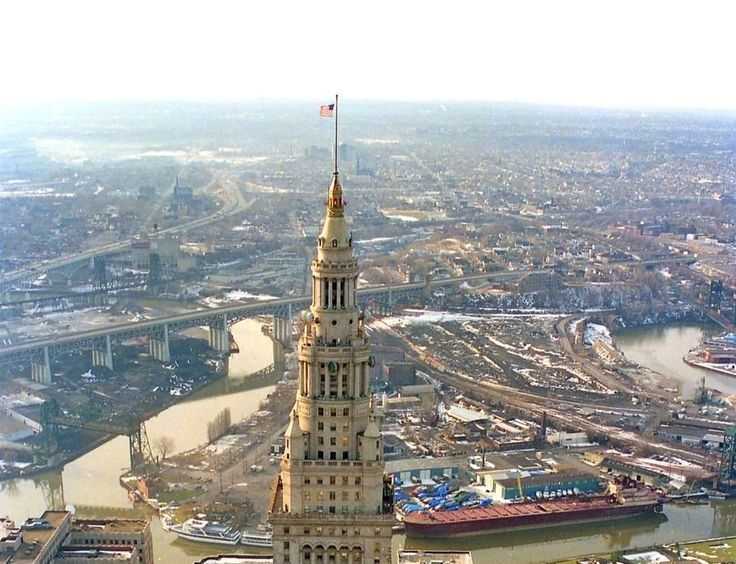
RELIC RENEWED The Terminal Tower has battled the harsh North Coast environment for80 years, and time has taken its toll. Ongoing repair and restoration work is underway toprepare the structure for coming decades.
The best address in the best location in the nation: 50 Public Square. So it’s been since 1928, when on 50 Public Square and ultimately rising 708 feet above it the Terminal Tower opened its doors. The $179 million price tag for what was originally known as Cleveland Union Terminal is dwarfed by the structure’s value as a Cleveland icon and the city’s most recognizable landmark. The dream of brothers Oris Paxton and Mantis James Van Sweringen was to be only 14 stories, sitting on top of the city’s rail hub. Instead the steel-frame structure, with decorative limestone and terra cotta exterior, topped out at 52 stories — atop 280-foot caissons — and when completed was the world’s second tallest building, behind only the Empire State Building in New York City. (As the two were built nearly simultaneously, the Terminal Tower reportedly was the world’s tallest for a few months prior to the topping off of its Gotham counterpart.) Today, as a Forest City Enterprises property, it serves as the centerpiece of mixed-use Tower City Center, with the entire Terminal Tower complex comprising 557,000 square feet on 34 acres.
Time took its toll
At 80 years old, the tower has battled the harsh North Coast environment for decades, and time has taken its toll. From floor 34 on up to the flag pole can be considered the Terminal Tower’s roof. Exposed to the elements for so long, the upper floors bore scars from water infiltration, including rusting steel that supported the terra cotta façade. Chunks began loosening and falling, with cornices failing and needing to be strapped into place, leading Forest City to assess and ultimately address the problems. In October 2005, the scaffolding went up from the 37th floor to the top so engineers could in effect “touch every inch of the façade” to determine the extent of water damage, according to Dennis Breiding, managing the renovation project for the Construction Division of Forest City Enterprises. Forest City brought in a structural engineering company, Barber & Hoffman Inc., of Cleveland, to study the problem, and tapped Provenzale Construction, also of Cleveland, to handle construction management as an extension of Forest City Construction.
“The original construction had trapped steel into the mortar,” explains Breiding, discussing the investigation phase prior to renovation work. “Steel flanges had rusted and expanded, acting like a hydraulic jack, and the expansion was tearing the building apart. Anything hanging would have to be torn off. We determined that the building was failing exponentially and we had to figure out how to stop that failure.”
Unique plan, unique methods
At that point, Forest City faced having to spend three years developing drawings and placing work out to bid — an extraordinarily long and expensive proposition. The decision was made, instead, to examine and fix the exterior floor by floor. With a $20 million-plus construction budget, Forest City, Barber & Hoffman and Provenzale teamed to investigate and develop bidding for nearly every area, according to Breiding. Essential for funding the project were historic tax credits. Receiving those credits required a unique presentation to state officials.
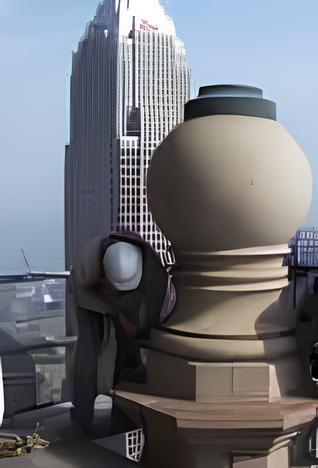
RELIC RENEWED The Terminal Tower has battled the harsh North Coast environment for80 years, and time has taken its toll. Ongoing repair and restoration work is underway toprepare the structure for coming decades.
“We didn’t have an exact renovation plan, but we knew what methods we would use to achieve it,” Breiding recalls.
Replacing terra cotta with terra cotta was no option, as the steel holding the terra cotta could no longer support the weight. The alternative: fiberglass cornices, with embedded aluminum extensions that would bolt to new steel. Lighter and easier to manufacture and install, fiberglass pieces would remain watertight and allow for removal of any heavy, hanging material. Architectural Fiberglass Inc., of Cleveland, was awarded the contract to supply the cornices and other fiberglass shapes for the project.
Liquid plastic, a coating often employing a fiberglass mesh component, was selected to repair terra cotta and waterproof the upper exterior.
Terminal Tower: Tackled Floor by Floor
The following floor-by-floor summary of exterior work completed or still underway during the renovation of the Terminal Tower, from a report compiled by structural engineering firm Barber & Hoffman, attests to the massive scale of this undertaking.
51st to 49th floor: replaced all mortar joints and replaced the 49th floor cornice with fiberglass; replaced deteriorated pieces of terra cotta and coated all terra cotta with liquid plastic.
49th to 48th floor: replaced all mortar joints and replaced deteriorated terra cotta on parapet wall while fully restoring the wall; replaced the 48th-floor cornice with fiberglass; coated all terra cotta with liquid plastic; installed new roof and vent.
48th to 46th floor: replaced mortar joints and replaced terra cotta on all 16 columns with fiberglass; restored ornamental iron on windows and replaced copper at column bases; replaced 46th-floor terra cotta cornice with fiberglass and coated all terra cotta and ornamental iron with liquid plastic.
46th to 44th floor: replaced mortar joints and deteriorated terra cotta pieces; replaced walkthrough concrete roofs and deteriorated walkthrough parapet walls; replaced 44th-floor buttresses with fiberglass and replaced concrete base; replaced buttress roofs; restored 44th-floor parapet wall; installed new roof and coated walls with liquid plastics.
44th to 41st floor: replaced 43rd-floor cornice; replaced mortar joints; replaced all 16 terra cotta columns with fiberglass; restored ornamental iron on widows and coated with liquid plastic; replaced deteriorated terra cotta pieces; replaced copper at base of columns and on 41st-floor cornice.
41st to 37th floor: replaced mortar joints and deteriorated terra cotta pieces; replaced copper on turret walls; replaced terra cotta with limestone on turret walls; replaced 37th-floor roof.
37th to 34th floor: replaced cornice stone and replaced steel lintels with stainless lintels; replaced mortar joints and deteriorated terra cotta pieces; replaced 34th-floor roof; replaced 34th-floor cornice with fiberglass; coated 34th-floor parapet wall with liquid plastic.
34th to 15th floor: replaced mortar joints; cleaned exterior; replaced caulk and deteriorated stone pieces; coated column capitals with liquid plastic; replaced 15th-floor cornice with fiberglass.
15th to 4th floor: replaced mortar joints and deteriorated stone pieces; replaced caulk; restored deteriorated balconies.
4th floor to ground level: replaced mortar joints and replaced deteriorated stone and terra cotta; replaced caulk joints.
Time to get to work
With historic tax credits granted, Provenzale sent out bid packages, the first being for scaffolding from the 37th to the 52nd floor, erected by January 2006 and becoming a familiar Cleveland skyline sight. Other bid packages included painting, patching and application of liquid plastic, replacement of 16 upper and 16 lower exterior columns with fiberglass, and replacement of decorative hanging terra cotta with fiberglass shapes, according to Dave Provenzale, who is handling the Terminal Tower project for Provenzale Construction.
Though differing in detail from floor to floor, the exterior renovation was summarized by Michael Mazzocco, a structural engineer with Barber & Hoffman, in a project report.
“The biggest problem encountered was water infiltration into the building,” he wrote. “To eliminate the water infiltration, mortar joints were cut out and replaced with new mortar [in fact, points out Breiding, beginning on floor 37 and continuing to the top of the building, every joint was crowned out], various deteriorated pieces of terra cotta and stone were removed and replaced, roofs were removed and replaced, and drains were repaired and/ or replaced and cleaned. The upper portion of the tower was coated with liquid plastics. Where the terra cotta was determined to be beyond repair, all material was removed with the underlying material, either concrete or steel, being restored. Once the material was removed, the concrete was replaced, steel was cleaned and painted, and new material was installed. Based on the extent of deterioration, it was decided to either use original material, such as stone or terra cotta, or replace with fiberglass replicas duplicated from salvaged material.”
As one of the first renovation tasks, crews toiled in rarified air, performing extensive repairs on the cast-iron cupola at the base of the flagpole. As originally constructed, the cast iron served as a form for poured concrete. Over the years, the cast iron had cracked and rebar in the concrete had rusted. Workers cleaned and restored ornamental iron or replaced it with new steel cornice and coated the iron with liquid plastic, replaced the handrail, cleaned the existing metal deck and coated it with liquid plastics, and replaced all cupola windows.
New computer-controlled LED lights ring the exterior at this lofty height. The new system can be programmed for roughly 30 presets and changed remotely for events such as baseball games, football games, holidays and more. The array of colors is almost infinite and there are plans to create one setting to mirror how the building looked in the early 1950s.
Great efforts were made to prevent water penetration. Water entry over the years had resulted in damage to interior walls on lower floors. A tour revealed the layers of materials and coatings placed to watertighten the entire exterior. But the work didn’t end with façade renovation. During this renovation, all 2,050 windows in the tower are being replaced to provide better insulating qualities and mimic the originals. In addition, all exterior surfaces will have been cleaned by project’s end.
Project gets a lift
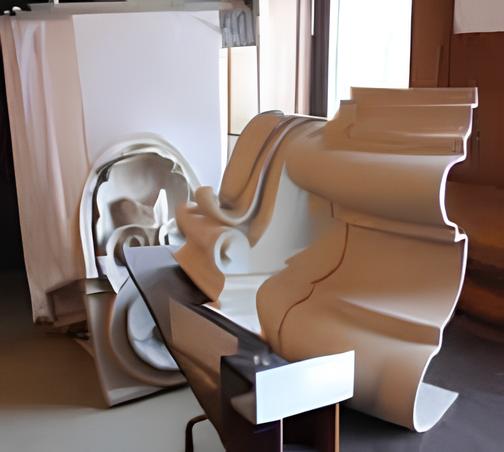
MATERIAL IMPROVEMENTS Fiberglass cornices and other shapes,supplied by Architectural Fiberglass Inc., were used to replace damagedterra cotta.
Renovation has not been limited to just the outside. Vertical access was addressed as Kone Elevators & Escalators, of Cleveland, spent more than three years modernizing 21 elevators, replacing controllers, hoist machines, hoist ropes, door operators, fixtures and other components. Cab interiors were remodeled, providing an appearance similar to previous interiors but with new wood trim and ceilings.
“The biggest challenge we encountered was safely removing the 1920s-era DC hoist machines from the mechanical rooms and out of the occupied building,” says Tim Clements, Cleveland branch manager for Kone. “Safety is obviously our number-one concern not only for the tenants but for our workers. The old hoist machines weighed in excess of 6,000 pounds. We had to break them down to pieces weighing no more than 3,000 pounds due to floor loads and the fact that the service elevator had a capacity of only 3,000 pounds.
“The existing hoisting equipment is based on inefficient technology, whereas the Kone elevators utilize the Kone EcoDisc hoist machine,” Clements says. “This permanent-magnet synchronous motor is 50% more efficient than traditional two-speed traction elevators.”
What's next?
Almost five years in, the Terminal Tower renovation is coming to an end, but Forest City Enterprises hopes to continue building on the momentum. The wish list includes restoration of the observation deck to its original grandeur as well as restoration of the Van Sweringens’ living space. But in the meantime a pat on the back is warranted.
“We beat the five-year timeline — ahead of schedule and under budget,” Provenzale says proudly in describing how the principals and subcontractors worked together to tackle this massive project.
And for Forest City’s Breiding, this project represents much more than just restoration of the company headquarters.
“This project is not only a city icon but also is our company headquarters,” he says, “and we are very proud of it.”